PROCUREMENT PURCHASING
As owner builder, you will want to employ the best practices in your purchasing - to use
procurement purchasing strategies that will enable a smooth work flow on the job site. Procuring the materials you need in a timely fashion requires planning and diligence.
You have already determined what you will need for your home building project and probably from whom you will buy. These topics are covered in Cost Estimate and Suppliers
' Quotes.
As you need materials (according to your updated Critical Path and in consultation with your subcontractors) you will write purchase orders and order them. Make sure you specify the quantity, description, and unit price of all materials you order.
WHAT ALL IS AFFECTED BY YOUR ORDER?
When ordering materials, try to think of everything that affects or will be affected by the item you are ordering. For example, when ordering counter tops, you need to tell the supplier the make and model numbers of the appliances you are going to use so that properly sized spaces can be provided to receive them.
PURCHASE ORDERS
The number one rule in any good purchasing strategy is to use purchase orders! You can get them at any good office supply store. Here's a generic form you can use "as is" or adapt to your needs.
The importance of "getting it in writing" cannot be overemphasized. It is a record of all the details of the transaction. Purchase orders are an integral part of controling your materials costs. More details on the use of purchase orders and what should be included in a purchase order can be found on our section on Cost Control.
VERBAL ORDERS
Verbal orders, either by phone or face-to-face with the salesman, are also a good idea - as long as they are backed up with a confirming written purchase order!
Verbal orders help answer any questions that are out of the ordinary. Talking with your salesman can help you tie down details and get a commitment on the delivery.
Verbal orders become a necessity when you come up short on some item and the subs are waiting. You'll even find yourself jumping in your car or truck to run pick something up that's desperately needed!
Just remember to follow that verbal order up with a written confirming purchase order, so that you "get it in writing!" You'll need the paper trail for your records.
LENGTHS
For lumber orders you will also need to specify the lengths required. For example, floor joists and roof rafters must be long enough to make the entire span required. They cannot be spliced.In other words, if lumber is quoted in board feet, it has to be purchased by quantity and length. For example: 38-2x6x14 would mean that you are ordering thirty-eight two by sixes, each of which is fourteen feet long.
DELEGATE!
If you do not want to be involved at this level of complexity (and many builders don’t), you can have the suppliers do the takeoff. You can let him worry about proper lengths and so forth.Just be sure that the supplier will make extra deliveries (sometimes called "fill-ins") if you are short any needed materials. Also make sure that the supplier will take back any unused materials in resalable condition, and that you won't be charged a restocking fee.
MEASUREMENTS
Modern suppliers should be selling materials in ordinarily understood increments - like linear feet, square yard, cubic feet, each, etc. Some however, may try to slip a board foot or worse yet a thousand board feet in on you. Don’t let this throw you. Just ask the supplier to translate these measurements into linear feet.
In case you missed the explanation on how you can convert board feet yourself in Suppliers' Quotes, here it is again. Take a few minutes and follow it through. It's not that complicated, really! And it is an excellent tool to have in your quiver.
TRANSLATING BOARD FEET INTO LINEAR FEET
A board foot is a piece of wood whose nominal* measurements are 1" x 12" x 12". The rule is to multiply the nominal dimensions together and then divide the answer by 12.
Example - for a 2x4: multiply two times four. The answer is eight. Divide eight by twelve. The answer is .67. Each linear foot of 2x4 has .67 board feet.So a 2x4 which is ten feet long has .67 x 10 = 6.7 board feet. Ten 2x4’s which are ten feet long have .67 x 10 x 10 = 67 board feet.
To convert board feet to hundred board feet, divide by 100. To convert board feet to thousand board feet, divide by 1,000.In our last example (ten 2x4’s, each ten feet long), you would have 67÷100 = .67 hundred board feet. Easy, huh?
Some lumber dealers like to price their lumber this way because that is the way they buy it. How about the example given earlier of the 38-2x6x14's. How many board feet is that? Answer: 2x6÷12x14x38 = 392 board feet.
Again, it may have been quoted that way, but you would order it by quantity and length.
*Nominal measurement means what the particular piece is called, which is really its rough-cut, unfinished size. For example, a 2x4 is actually 1-1/2" x 3-1/2." "Nominally" it is a 2x4.
MARKING THE LOT
It is important that the owner builder
mark the home building lot clearly with a sign that shows where the materials are to be placed. The sign should be visible from the road. Give the lot and block number of the lot and the address if you have it.
Also, certain materials need to be placed in certain locations when they are delivered so that they will not have to be moved unnecessarily. For example, the bricks for the foundation walls should not be unloaded right where your footings are to be dug!
Being there when the materials arrive, or putting a sign (“Put Bricks Here”), will solve this problem before it is a problem.
RECEIVING AND STORING MATERIALSReceiving materials is the other half of ordering. We cover this important subject in
Cost Control. Proper receiving is an important part of your relationship with your suppliers.
Don't neglect it!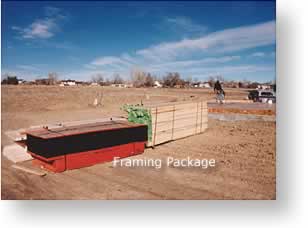
THINKING AHEAD
When you did your Schedule Planning, you were working somewhat in a theoretical world. Now your scheduling will be real world, indeed! Your biggest job will be in training yourself to always think ahead two or three steps.
When your framing starts, you should be lining up the electrical, plumbing, HVAC, and insulation work. When these are in the works, you’ll be lining up your trim.Get your subcontractors out in advance, and make sure they remember what it is you want on your home building job. They may have done several other jobs since quoting yours. And everyone doesn’t have a perfect memory or keep completely accurate notes.
Your schedule planning will help you stay on top of it. Just remember this cardinal scheduling rule for successful home building:Don’t wait until one job is finished before you schedule the next.
A good owner builder is always working not only with today’s subcontractors and suppliers, but also those who won’t come into play for two or three weeks.
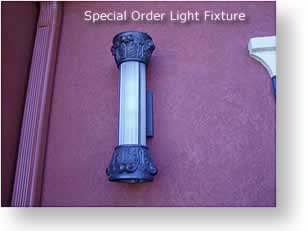
SPECIAL ORDERS
Be especially vigilant to allow more than the allotted time necessary for special order stuff to be acquired by your suppliers. Examples may include custom window sizes, "specialty" hardware, non-stock brick, etc.
If your supplier says it will take six weeks, tack on a few extra weeks to be on the safe side. Even so, you may experience unavoidable delays with special order items. So don't be surprised. There are lots of surprises in home building. As an owner builder, you have to be ready to roll with the punches.
Moving On
Another area of Construction Management responsibility for the owner builder is Scheduling (the day-to-day variety). Click here to go to Scheduling or here to go back to Construction Management.